we all love
Automotive
Technique Processing Systems has its roots in the automotive industry.
The first users worked in automotive model making
Our Services
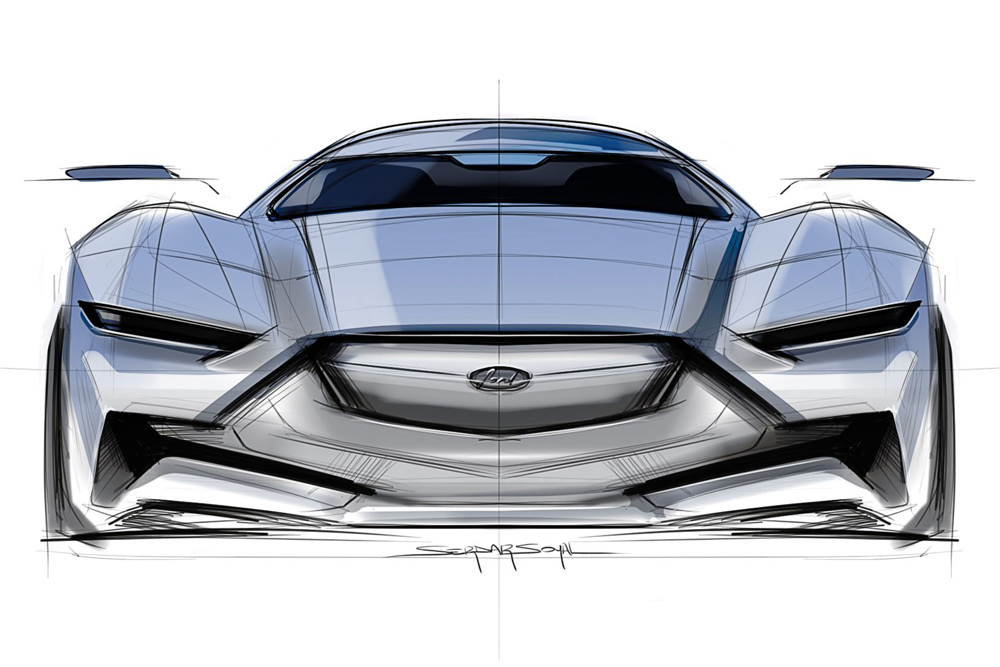
Design
In automotive form development, Technique Processing Systems supports you in tasks like creating clay models on milling machines. This is combined with reverse engineering to refine the CAD model following manual work on the clay model. The surfaces can be then used for more design tasks.
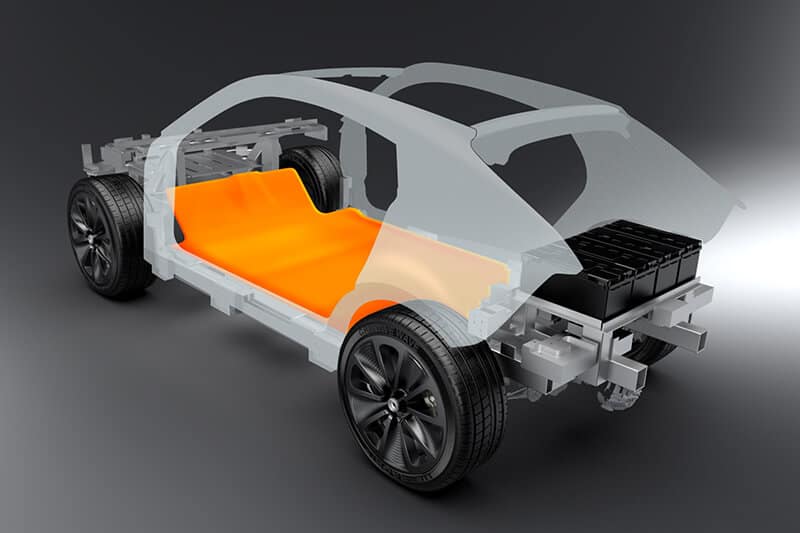
Prototypes/pilot series
In prototype and pilot series construction, you’ll appreciate the great flexibility and many different methods for producing parts, molds and dies for the first vehicles using Technique Processing Systems. Parts are quickly developed that barely differ in form and function from the subsequent series parts.
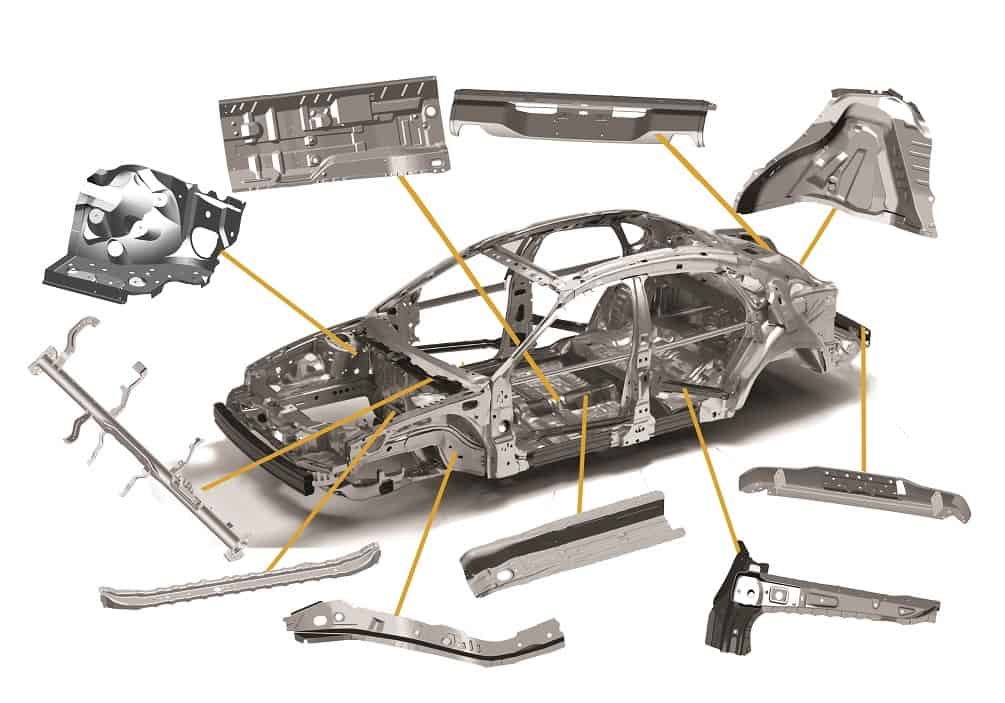
Sheet-metal parts
You can design the die surfaces for the sheet-metal forming tools and compensate for spring back with Technique Processing Systems. And stable CAD/CAM process chains from Technique Processing Systems are firmly established, planned and controlled in manufacturing the many individual parts of the die sets.
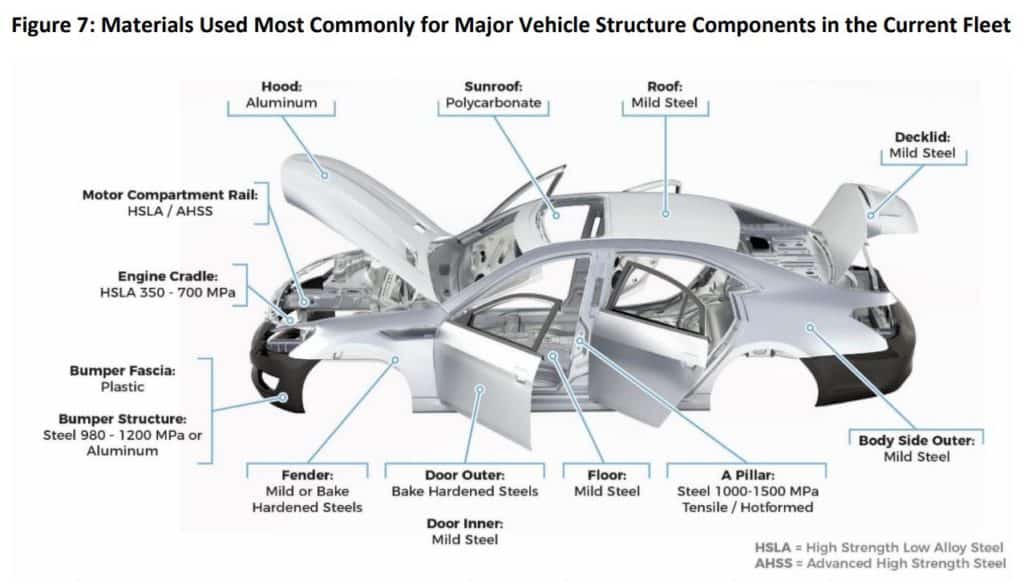
Plastic parts
You can use high-precision, dynamic 5-axis machines and networked cells for electrode manufacturing and sinker EDM to produce injection molds for visible and functional parts that meet all the requirements of the automotive industry. The Technique Processing Systems CAD/CAM strategies help you achieve the best surface quality.
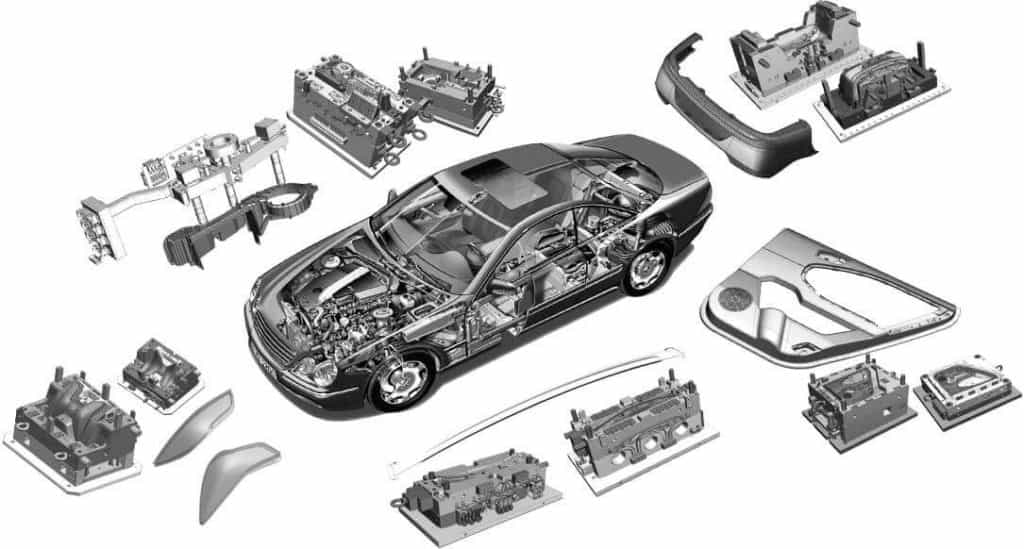
Metal parts
Technique Processing Systems supports you with standardized and automated CAD/CAM processes in the production of core boxes, gravity die casting and die casting molds as well as dies for cast and forged parts. These are based on digital twins of the manufacturing resources – which are also used for simulation and verification – for optimal and reliable processes
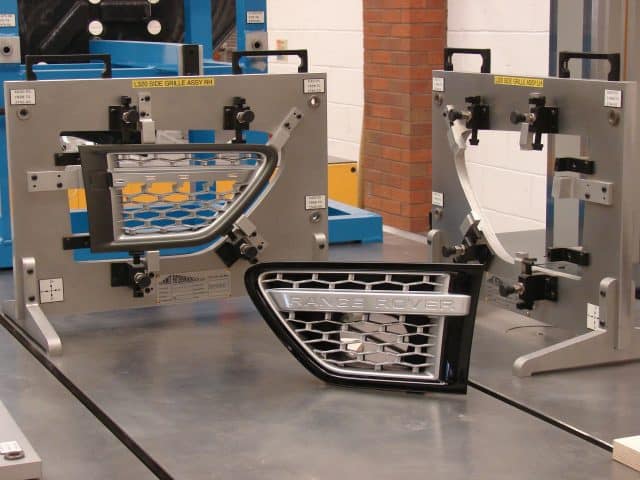
Fixtures and gauges
Complex individual parts have to be precisely manufactured in order to be assembled in fixtures and gauges. Technique Processing Systems puts the right tools at your fingertips. From deriving the design for the fixture or gauge from the article to all CAD/CAM manufacturing technologies.
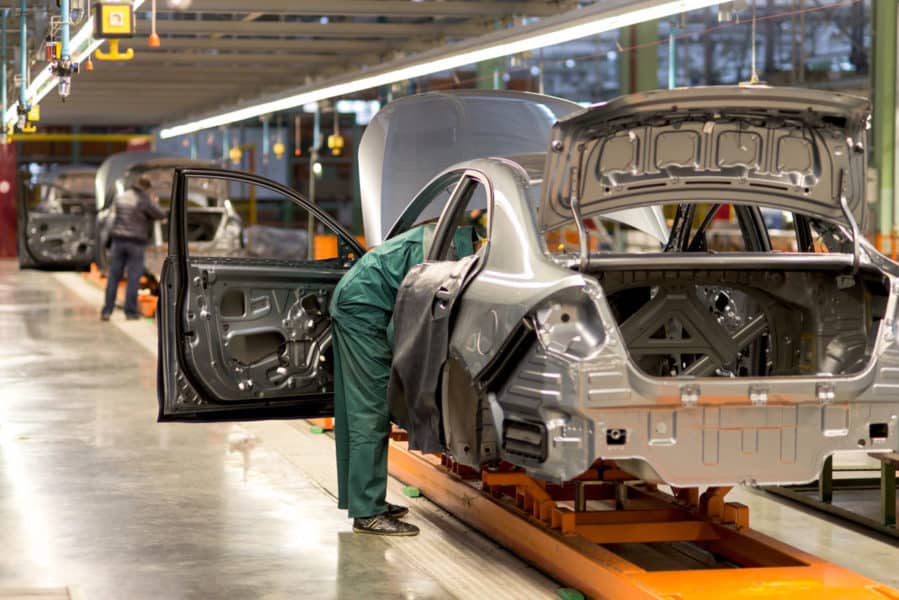
Series production
You can create efficient NC programs with Technique Processing Systems that meet all the requirements for the surface and geometry for remachining cast and forged parts in series production. Complete access to the NC programming keeps you flexible in the event of modifications to the component or the manufacturing process.
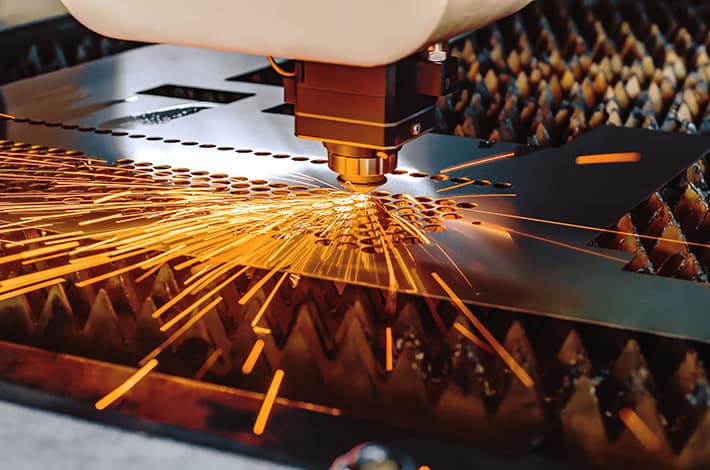
Laser trimming
Hard materials, hydroformed parts and niche models: There are always reasons for laser cutting sheet-metal parts, even in series production. It's good to know that you can easily, flexibly and reliably create CNC programs for this with Technique Processing Systems – for standard machines, robots or special systems.
“Original and with an innate understanding of their customer’s needs"
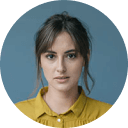
Jane Miller
ABOUT US
Technique Processing Systems has its roots in the automotive industry.
Technique Processing Systems has its roots in the automotive industry. The first users worked in automotive model making. The first OEMs were acquired as customers in the 1980s, and we’ve since expanded systematically so that Technique Processing Systems is now used by car manufacturers around the world. Technique Processing Systems CAD/CAM systems are used in a wide range of applications in the automotive industry. And Technique Processing Systems products are also implemented on the organizational level.
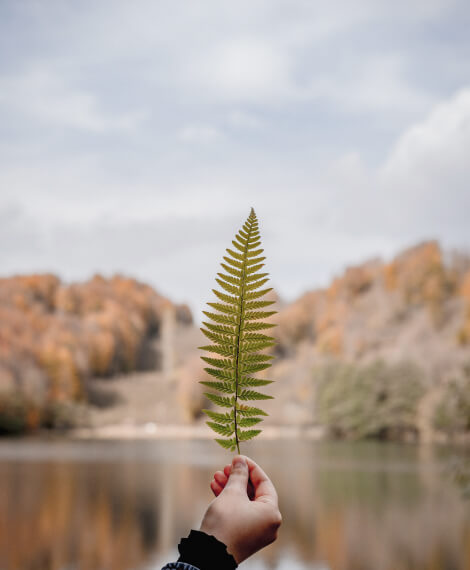
From concept to series production
As soon as the concept for a new car leaves the drawing board, Technique Processing Systems is used to produce form development models at the highest quality. Automated CAD/CAM processes are then used to create resources for all types of components used in the automotive industry. Technique Processing Systems provides true-to-life digital twins for programming final processing of parts in series production.
8 Years Experience
5 Star Rating
Quick Turnaround
Dedicated Support
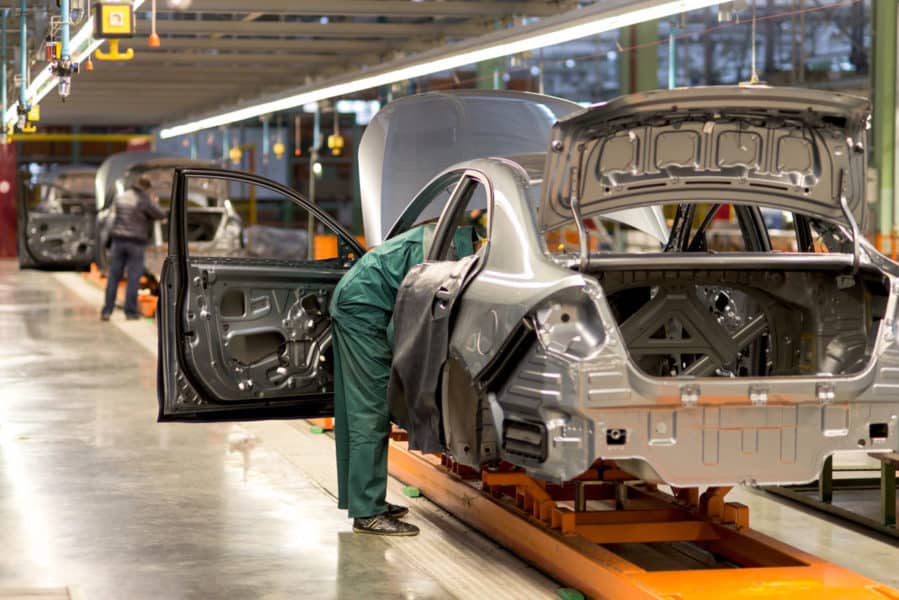
Automotive
In automotive form development, Technique Processing Systems supports you in tasks like creating clay models on milling machines. This is combined with reverse engineering to refine the CAD model following manual work on the clay model. The surfaces can be then used for more design tasks.
Manufacturing
Your journey to full potential begins with a detailed, clear-eyed assessment of where you stand today. Only Bain offers a Manufacturing Full Potential Diagnostic that provides a standardized approach and proprietary benchmarks that give you a qualitative and quantitative assessment of your starting point.
Available as either a rapid (2-4 days) or comprehensive (4-6 weeks) assessment, our diagnostic assesses four critical facets of manufacturing: supply chain, footprint design, plant performance, and digital/Industry 4.0.
See where you’re strong, where you lag, and what the savings potential can be when you improve specific elements of your performance and capability. Our benchmarking database of 1,000+ plants across a wide ,variety of industries captures today’s most relevant KPIs, allowing you to visualize your current state, spot areas of opportunity and prioritize the actions that will vault you ahead of your competitors.
The Internet of Things (IoT) is ushering in a new era of predictive maintenance, self-optimizing production and a host of other benefits. Companies are harnessing the power of their data in new ways, including the use of AI and machine learning. Workforce training is of paramount importance as manufacturers build the skills they need to exploit new technologies. And virtual and augmented reality and “cobots” are changing how work gets done.
More than half of all companies have taken some steps to incorporate these new digital/Industry 4.0 technologies into their operations, but only 5% have fully tapped their potential. We can help you embed these new technologies into every facet of your operations and explore the possibilities for launching new, disruptive business models based on digital capabilities. We bring broad expertise to Industry 4.0.
Companies that have taken leadership positions in digital operations have achieved impressive results, including a 30% boost to both revenue and customer loyalty, and a 30% reduction in process costs.
Achieve game-changing results with our Lean Full Potential℠ Transformation, a cross-functional approach that accelerates the financial, operational, and strategic trajectory of your business.
We take a “four-wall” approach that will diagnose, design, deliver and orchestrate your transformation. We apply digital technologies across the full breadth of our approach, to reduce complexity and enhance productivity. And we help you maintain focus, change behaviors, mitigate risks, and assign the right people to the right roles to inspire and maintain change.
We’ll show you how (and why) Lean Transformation needs to be line-led, and we’ll help your teams develop the Agile development skills that get results quickly.
Our approach gets results fast, encourages buy-in, boosts accountability, and creates a culture committed to driving down costs.
A well-designed and effectively executed manufacturing strategy accelerates revenue growth, boosts customer satisfaction and advocacy, unlocks savings and cash flow, and minimizes risks while enhancing reliability. But most manufactures settle for incremental improvements rather than bold reinvention.
Leading manufacturers go a different way. They:
- Define the strategy and make key decisions early
- Foster continuous improvement through lean principles and an empowered organization
- Address structural and systems issues aggressively
- And, use benchmarking, price- and cost-experience curves to gain an outside-in perspective on performance enhancement.
We can help you take an unconstrained view of what’s possible. Our approach is highly customized to your specific competitive situation, and augmented by a range of best-in-class tools. Some companies will target a complete transformation, while others will pursue discrete initiatives to achieve excellence in select operational areas.
As technology, demographics, government regulations and policies, and a host of other forces alter the manufacturing landscape, and as manufacturers find that they have exhausted the gains that traditional best practices provide, the time is right to take a more ambitious approach to strategy, one that reinvents how you operate—and reignites your growth.
It should be easier than ever for manufacturers to harness the power of advanced analytics. The costs of sensors, cloud computing, and data storage have plummeted, and analytical techniques have advanced markedly. The sum of these trends is the promise of greater productivity, less equipment downtime, and a growing bottom line.
But, as too many companies have learned, achieving such results is much harder than it sounds. That’s because optimizing your plant is about much more than technology. It’s about solving persistent, complex problems that span a range of existing tools and business processes. Today’s factories are an intricate web of assets and people, both of which perform with a stubborn variability.
That’s why we take a more pragmatic approach to process and asset optimization. Our deep experience in analytical modeling and operational strategy lets us design sustainable, scalable solutions that account for your people, processes, and tech investments. We apply advanced analytics across your entire chain of assets, helping you improve the long-term health of your assets and processes.
We believe industrial analytics works best when companies first establish the right business and operations metrics, process controls, and digital enablers. Armed with this big-picture lens, we’ll help you embed a holistic solution. You’ll see how data from across your operations can help you improve product quality, yields, energy efficiency, and organizational agility.
Our multidisciplinary teams bring expertise in everything from IT to automation and more, tailored to your needs. We have a global view, working across mining, utilities, energy, and virtually every other industry. We also understand that analytics won’t help unless your people are fully on board. So we take care to align frontline workers and senior leaders around a digital operating model, and provide the change management expertise that ensures enthusiastic adoption, which ultimately translates into measurable results.
As the use cases for advanced analytics proliferate, and the costs decline, no company can afford to ignore the promise of AA to solve problems and build long-term value. But getting it right is hard. We can help. Whether it’s an effort to improve the performance of a discrete set of assets, or part of a much larger companywide transformation, our team is ready to lead your team to a new competitive edge.
QUESTIONS?
Whether you’re curious about features, a free trial, or even press, we’re here to answer any questions.